Successful controls integration can be a challenge in both new construction and renovation projects. Laboratory facilities present unique challenges with critical lab spaces and non-lab areas that include both traditional building automation systems (BAS) and packaged laboratory controls.
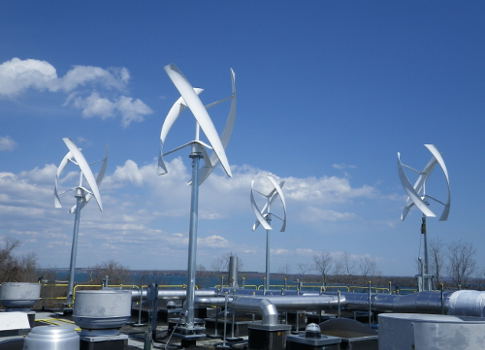
Learning Objectives:
- Understand the steps necessary to ensure controls integrations across all building systems are functional, ensure occupant safety, and allow for energy-efficient operation.
- Review the commissioning services provided to ensure proper system operation per the contract documents.
- Understand the various ways to save energy using control systems in laboratories.
Integrated controls can be a challenge in both new construction and existing buildings. Laboratory facilities, in particular, present unique challenges as they contain critical lab spaces and non-lab spaces, which include both traditional building automation systems (BAS) and packaged laboratory controls.
In some cases, laboratory control systems are left to be stand-alone with only basic alarming capabilities. If a system isn’t fully integrated, owners will face safety, reliability, and efficiency challenges that have to be immediately addressed. Whether the facility contains biological, chemical, animal, or physical lab spaces, all are critical areas where occupant safety is the No. 1 goal. OSHA defines engineering controls as one of four of the "hierarchy of controls" in dealing with workplace hazards. Whether laboratories controls are integrated into a BAS, they must be functional and must protect the occupants.
Whether integration is required for advanced monitoring or is used as a means for additional levels of controllability in the name of energy savings, integrating anything and everything is now standard practice. However, automation systems and systems integration don’t happen magically. Be it by BACnet, Modbus, or another protocol, system integration needs to be properly designed, specified, and reviewed during both the design phases and submittal reviews to be successful. Incorporating commissioning services early in the design phase and carrying through the construction phase of a project adds another level of assurance that a successfully integrated system will be turned over to the owner.
Integrated control systems
Many owners with nonintegrated laboratory systems are perfectly happy to leave them that way. They use separate computer interfaces to access each building system individually. Although this is an acceptable method of accessing the building data, there is lost opportunity not only for potential energy savings, but also for capturing opportunities to identify preventive maintenance tasks or quicker responses to system failures or faults. Having an integrated system accessible via Web-based laboratory dashboards, tablets, or phones is now commonplace and a standard technology for system monitoring.
Whether performing a new system design, recommending system improvements during an energy audit, or executing a re-commissioning or retro-commissioning effort, owners and engineers should always look for opportunities for energy reduction and potential energy savings. Through extensive integration between traditional BAS and localized laboratory control systems, energy-saving measures—such as supply and exhaust air static pressure reset, standby and occupancy control, and temperature-reset strategies—can be implemented. Without the full integration of the labs, none of these measures can be successfully implemented; the systems will be unable to save the maximum amount of energy.
Fully integrated systems also present an elevated level of safety. Stand-alone laboratories can pose safety issues if room pressurization is lost and building operators are unaware of the problem. Stand-alone labs commonly have fume-hood low-velocity alarms, but oftentimes, airflow tracking and zone pressurization are not alarmed. When building operators have multiple systems, they are responsible for reviewing and maintaining their daily monitoring procedures. Because of the complexity of the management of the systems, operators can become lax over time.
Although it varies based on the type of facility, many building operators are more concerned with human comfort than laboratory safety. An operator will immediately adjust controls based on a hot or cold occupant complaint but may not look for laboratory airflow or pressurization issues, frequently because they don’t even know what to look for. Fully integrating a laboratory controls system to the same operator terminal as the rest of the building gets operators into the habit of reviewing all of the systems onsite. Automating laboratory alarming also adds an additional level of occupant safety.
In the more advanced laboratories, there are energy-driven reasons to integrate building and laboratory systems. Control strategies—such as supply and exhaust air static pressure reset—are used by linking laboratory terminal equipment differential pressures or damper positions back to central air handling units (AHU). By allowing for static pressure reset at the air handlers, there is typically instant savings in fan energy. Of course, safeties are built into the control logic to allow for fail-safes, ensuring that laboratory airflows are never compromised.
Design considerations
Successful controls integration starts with a well-documented owner’s project requirements (OPR) and design effort for a new facility or a renovation. More often than not, the controls and sequencing are among the last components to be addressed. For example, modifications are often made to the specifications at the last minute, and oftentimes, the control schematic drawing points list isn’t developed until the end of the job.
RMF Engineering has commissioned projects where all laboratory integration was removed from the project as a value-engineering measure to save cost. What was lost as a result were opportunities for integrating systems as a means for energy savings, not to mention providing any BAS interface to the laboratories to allow facility operators to monitor lab operation. What was saved in implementation cost was lost in energy savings and proper access to the system. These are elements that need to be considered sooner rather than later. Failing to identify the desired interoperation of the various systems early on in design will lead to a lack of communication between different control systems.
While developing a basis of design (BOD) for a project, all interoperation must be defined. At this time, systems and equipment need to be selected that can meet the project goals. This is standard operating procedure for most system designers, but if you consider product selection from a building automation point of view, you will see this process in a different light. Laboratory control systems will come with different features and varying levels of integration.
Control systems typically come with their own proprietary software. While one vendor’s software, by default, allows for a high level of BAS integration and controllability by exposing all available control points, another vendor’s software may lock out those same points and make them read-only as a safety precaution and include a requirement for manual exposure of those same control points. While one laboratory controller may allow for occupied or unoccupied control only, another may allow for additional modes such as "standby."
The desired interaction of the BAS and the laboratory controls system must be clearly understood so proper equipment selection can occur. OPR or BOD documents must be made available and should be developed with the owner. Clear direction for the project, be it new construction or an existing building, must be identified so proper identification of integrated systems can achieve both system operation and energy-saving goals.
Design review
To ensure successful systems integration, there must be extensive review during the design phase of any project. Many of the common design oversights can be caught with a proper and focused review. A quality analysis/quality control (QA/QC) review must be conducted.
The goal of the QA/QC review for the design group is always the same: There should always be a complete set of contract documents and appropriately specified controls integration.
System designers should begin by reviewing the OPR. This is followed by a review of the specifications. Every section that could possibly be tied into the BAS should be reviewed, starting with the controls section. This is the most logical place to begin and start identifying integration requirements, and this is where the holes in integration are first discovered.
Designers should keep in mind that from the perspective of a commissioning authority, it is rare to find relevant specification sections or requirements sections that are thoroughly identified. Laboratory terminal units, heating or cooling plants, lighting control, power generators, etc., must all be clearly defined in both the specifications and drawings. It is critical that system designers thoroughly review all documents during the design review to ensure that there aren’t missing related specification sections or references to integrated systems.
After the control specification has been reviewed, all other equipment-specification sections need to be reviewed. Once again, a review of the related specification sections or related requirements sections should be performed to see if the controls section has been referenced, though in many cases it is not. Many times, owners may find phrases randomly placed in the spec, such as "shall connect to the BAS" or "will report to the BAS."
Rarely in the individual equipment specifications will you find coordinated communication protocols with the controls specification. When requirements for integration are provided, they typically are generic. While it may be enough to say that a system should be provided with BACnet capability, there is a chance that when equipment submittals come through, some equipment will have BACnet/Internet protocol (IP) communication cards while others are provided with BACnet/master-slave token-passing (MSTP) communication cards. In this situation, the desired integration at the end of your project will still function, but at an additional cost.
The bottom line is that rarely do specification sections identify how a BAS will be interconnected or integrated.
Once all specification sections have been reviewed, documenting both specific and implied forms of controls integration should be completed. A specification that includes a BAS points list should be tabulated for future comparison to drawings and submittals. When applicable, the integration type is recorded as well.
The next step is to review all project drawings. The review cannot be focused solely on the control flow or sequence drawings, but multiple disciplines must be reviewed in their entirety. This full review is necessary to pick up items, such as fire alarm integration or utility metering—the two most common points of integration that are skipped over. For example, designers can find plumbing drawings with a note that a water meter shall report to the BAS, but that point is not picked up in the control drawings.
After the completion of both specification and drawing reviews during the design phase, the design team will have an internal review document that identifies integration types and desired integration points. If a points list was included with the specification, the team also will have a side-by-side comparison of BAS points across both contract documents. With that information available to them, designers can easily visualize where holes in the BAS integration design are occurring.
Construction phase
Although it feels as though the bulk of the integration review is conducted prior to implementation, there is a definite need for continued review throughout the construction phase of the project. Understanding that systems can be properly integrated is one thing, but taking the proper steps to ensure that a usable system will be provided to the owner is another.
The next step of the review process occurs when submittals begin to arrive. Traditionally, the equipment submittals arrive first, followed by the building automation submittals. The document the designer created with spec and drawing points lists should be fully populated with points listed in the submittals. The control submittal carries with it the bulk of the data. While the controls submittal is oftentimes a cut-and-paste version of the contract drawings, a full-team review is still required. The network riser diagrams will outline whether all desired components have been accounted for, and the individual system flow diagrams and points lists will outline whether all the desired integration points are present. Conducting a final review of each of those components is key to a successful implementation phase. It’s recommended that an individual is specifically tasked with conducting it rather than having multiple team members trying to coordinate review.
It can be a challenge to ensure that each piece of equipment is selected with the proper communication protocols that will communicate with the BAS. Finding equipment submittals in which the communication protocol is clearly identified can oftentimes become difficult. Some of these submittals will list the types of protocols available, but the option that is being provided is not highlighted. If a submittal identifies that a chiller can communicate via Modbus, BACnet/IP, or BACnet/MSTP, they must clearly identify which communication card they are providing with the chiller.
If a specific part number for the communication interface is not selected, it isn’t complete. When in a construction administration role, it is best practice to have the contractor revise and resubmit to clearly identify communication protocols supplied with the equipment. When in a commissioning role, providers should note that supplied protocols should be provided and that the contractor is responsible for coordinating the integration effort to ensure that the design intent is met.
In the case of integration of laboratory controls systems, it’s important to spend extensive time reviewing the software and features associated with the submitted hardware. If the submittal is not provided with a table of read/write points of control, then the engineering team should ask for it. This is one of the last opportunities to ensure the design intent and OPR are achieved and a usable system is going to be provided to the owner. Make sure the desired integration points are not only readable, but also make sure any writable points that are integral to the sequences of operation are present.
This is the point in the process where designers will benefit from holding a controls-integration meeting. At the meeting, the owners, designers, and contractors will thoroughly review the project to discuss communication-protocol types and verify that all desired integrated components have been picked up in the contract documents. This is an opportunity for the designer to ensure that the project team understands what to look for when submittals are provided. For instance, during the submittal review, the project team should look for the type of BACnet protocol that is being provided. If this is not done during this stage, there will certainly be issues during implementation.
As an example, a piece of equipment that is supplied with a BACnet/IP communication card will interface with a BACnet/MSTP interface, but not without an additional piece of hardware. Rarely do we see this level of communication identified in the specifications, and this is the last chance to ensure the proper components are provided. This additional piece of hardware will likely come at an additional cost for the part, labor to install it, and labor to program and integrate the associated points. Addressing these items at this stage will allow for a streamlined implementation during the construction or renovation phase of the project.
Proper data management is key to system operation. There are additional data, and additional stress, on a building automation controls network that comes with laboratory integration. The data must be managed during implementation to prevent slow BAS access.
Designers should assist in determining which available integration points from the laboratory controllers should be accessible from the BAS to meet all project and OPR goals. All available data points should not be integrated—the process should be determined by requirements of the sequence of operation and the experience level of the owner.
A critical step involves working with the controls contractor to ensure that change-of-value (COV) rates are properly set to reduce network traffic while providing useful real-time lab data to the owner. COV rates are essentially refresh rates of the data displayed on the BAS server and within the graphical user interface. A laboratory controller will update data on the BAS server based on the COV setting. If a COV is set to 0.1 cfm on an airflow measurement, for instance, the laboratory controller will update the BAS over the network for every 0.1 cfm of change in reading. The lower the COV setting, the higher the rate of data exchange across the building automation network; thus, the slower the network responds. Reviewing trending capabilities and setting limits on data retention that make sense for that particular site and application should occur during the commissioning process and final review of system operation.
Focusing on energy efficiency
While most laboratories are focused on occupant safety, not all laboratories are focused on energy. One of RMF Engineering’s clients, in particular, has used its facility data (which is integrated from the laboratory controllers to the BAS) to monitor lab performance and ensure energy standards are being maintained. Using integrated airflow rates and a table of room dimensions, they are calculating real-time air-change-rate metering as a means to quickly see if the targeted 8 and 4 air changes/hour are being maintained. Using integrated room-occupancy sensors, they allow for standby modes of operation during their daily occupancy schedule to reset airflow rates to unoccupied flows while maintaining lab temperature and humidity set-points. Using integrated differential-pressure transducers, they are resetting the AHU supply’s static pressure set-points.
These energy-monitoring and -savings features would not have been possible without the proper integration and usability of the client’s BAS and laboratory control modules—and without established owner requirements and focused controls integration review.
An added benefit of the successful integration at this facility was the final layer of a laboratory-monitoring dashboard. Due to the nature of this facility and the structure of its service contracts, implementation of the dashboard was a risk to network performance and system reliability. Careful monitoring and data management of the integrated system points were crucial to the successful installation of the system and to ensure the established existing system reliability was maintained. The main issue the team wanted to avoid was taking a functional building and lab control system and slowing the network down by adding this additional layer of monitoring.
When the client decided to install the laboratory dashboard, RMF Engineering was tasked with monitoring the implementation as it coincided with a simultaneous re-commissioning effort. The re-commissioning effort included a 33% sampling rate of all laboratory spaces within the facility. While functionally testing the laboratories, RMF coordinated using both the existing BAS as well as the newly implemented dashboard. In using both control systems to test a laboratory, RMF was able to more clearly identify who was needed to resolve the issue when an issue arose. The synergy between the two projects simplified monitoring network speeds during other onsite efforts and provided multiple systems to use during operational checks.
At the conclusion of the project, the dashboard was successfully rolled out to 280 laboratories and 9,000 data points. These data points include air and temperature values, their associated operating set-points, heating-valve position, trends, alarms, and air-change-rate calculations. All 9,000 points are integrated from the lab control system to the BAS and the laboratory dashboard. Roughly 2,800 of those points are trended by both the BAS and the dashboard, which is a significant amount of data passing along the building control network.
It was critical during the course of this renovation project that no disruptions to active research occurred — therefore, access to all system data had to be maintained at all times. The re-commissioning process of the facility found no impact on the building control network. This could not have been achieved without careful attention to data point mapping and trending across all systems.
Commissioning providers must have the opportunity of a design review to highlight system discrepancies or deficiencies and assist in driving a more thorough and complete set of contract documents. It allows for customers to experience not only a safe and functional laboratory facility, but also an energy-efficient one.
The key to a successful controls integration, whether it is in a laboratory environment or any other type of facility where multiple control systems exist, is to conduct a focused controls integration review. If a project schedule does not afford the time to conduct a review of this type, it will show when it’s time for installation.
Jeremy Bartlett is a commissioning specialist with the Field Services Division at RMF Engineering. He is a controls engineer with more than 10 years of experience working with building automation systems.