MEP upgrades, new construction: The Ohio State University RDJ MEP Upgrades and South Campus Central Chiller Plant; Engineering Economics Inc. (EEI)
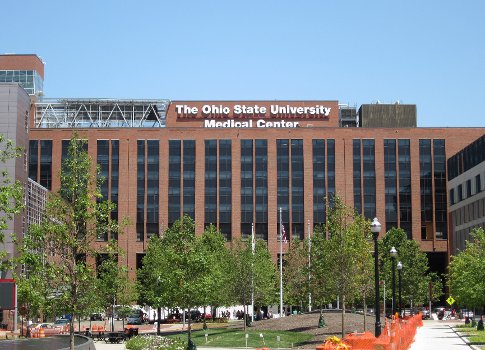
Project name: The Ohio State University RDJ MEP Upgrades and South Campus Central Chiller Plant
Location: Columbus, Ohio
Firm name: Engineering Economics Inc. (EEI)
Project type, building type: Commissioning, retro-commissioning of existing facilities, MEP upgrades, and new construction, hospital
Project duration: 5 years
Project completion date: Dec. 2013
Project budget for mechanical, electrical, plumbing, fire protection engineering only: $3 million
Engineering challenges
EEI was retained by The Ohio State University to provide commissioning services for the MEP upgrades project comprising Rhodes Hall, Doan Hall, and James Cancer Hospital (RDJ) at the Wexner Medical Center, as well as the South Campus Central Chiller Plant at the Columbus campus. As part of the project, major mechanical and electrical systems were in need of replacement in order to achieve several goals, including increased patient comfort and energy efficiency, current code compliance, and future capacity. As this is a 24/7 operating medical center, new major equipment was placed in service to limit outages.
Eight air handlers (15,000 to 90,000 cfm) were replaced in a just-in-time manner. These AHUs serve critical areas such as patient care, operating rooms, and the emergency department. Within Rhodes, poorly performing constant volume dual duct terminal units with pneumatic controls were replaced with variable volume direct digital control terminal units with hot water reheat. Electrically, several modifications were made to the emergency power system, including adding and replacing aging automatic transfer switches for improved reliability. The South Campus Central Plant supplies chilled water to the Wexner Medical Center, which consists of several buildings, built over numerous phases and without adequate documentation of how the chilled water was distributed and configured. EEI documented the entire chilled water system.
Additionally, EEI recommended final solutions for chilled water system modifications to address both peak usage and winter optimization, while finding a variety of undocumented conditions. These included variable flow control systems connected to constant flow pumps with no flow regulation; systems in an unbalanced condition with excessive or inadequate flow; un-pumped chilled water coils; and undersized pipe with excessive connected loads. The Medical Center is one of several buildings that connect to the new 30,000-ton South Campus Central Chiller Plant. Initially built at 20,000 tons, this N+1 plant will deliver 42 F chilled water with 5,000-ton capacity available on stand-by power in case of a power outage. When the chiller plant project was originally conceived, it was to be built concurrently with a major high-rise hospital addition. This high-rise addition afforded EEI the opportunity to functionally test the new chiller plant under various loading and staging scenarios with no impact to patient care.
Due to a variety of schedule and budgetary issues, the decision was made to commission the chilled water plant with live load from the existing Wexner Medical Center. To further compound an already complex situation, the construction team consisted of four engineers, two construction managers, and five mechanical contractors striving for one completion date with a fully coordinated design and implemented solution. In addition, the condition of the existing chilled water system degraded to a point where conversion to the remote plant became a necessity. EEI developed step-by-step procedures for converting from local to a remote chilled water plant while minimizing the impact of interruption of stable temperature and humidity conditions in patient care areas during peak cooling season in central Ohio.
Solutions
As a result of the Wexner Medical Center requirements to minimize utility downtime and mitigate construction activities that impact patient care, EEI was challenged with developing a just-in-time testing strategy for AHU replacement. Working closely with the engineering and construction teams, strategies were developed to allow equipment start-up, temperature control checkout, and life safety shutdown with fire marshal sign-off prior to connecting the new equipment to the existing system through the use of well-placed duct bypasses or run-around loops. EEI provided pre-functional test verification which included sensor and device calibration, setpoint verification, safety interlock verification, alarm setup verification, and sequence control prior to the final equipment cutover serving patient care areas.
During the conversion, EEI worked closely with the test, adjust, balance (TAB), and temperature control technicians to optimize setpoints and verify equipment capacity in normal and emergency power configurations. Using a combination of existing engineering documentation, staff interviews, and extensive field work, EEI created one-line diagrams for the multi-RDJ complex. This was especially challenging considering the 40+ years of chilled water system modifications to Doan Hall, restricted ceiling access, and missing pipe identification labels. As part of the study, EEI recommended converting the constant volume systems to variable volume for improved performance and energy efficiency and separating the process cooling equipment into disparate pumping loops. EEI and the engineer of record were able to establish separate process and AHU pumping risers for the East and West Doan Hall while utilizing the existing pipe risers, thereby minimizing construction costs and renovation impacts. In review of alternative strategies and in light of the success with the AHU conversion strategy, a similar plan was implemented for the chilled water system.
Utilizing the chilled water decoupler (a hydraulic bridge for decoupling pumping loops) and a plate-and-frame heat exchanger to isolate the high-rise system static pressure from the rest of the campus loop, the chiller plant will be started up and checked out by the industrial controls integrator through site acceptance testing. Using the Wexner Medical Center pumps, the control system will stage the chiller plant base on chilled water flow (high flow, low delta-T) and chiller amperage (low flow, high delta-T) through careful manipulation of the control systems. As the only common chilled water team member, EEI was often the single point-of-contact responsible for conveying information from one contractor/engineer to another. The conversion from local chilled water plant to remote chilled water plant is scheduled for August 2012.
This is a very high-profile project due to the importance of maintaining reliable and ongoing building cooling performance during the conversion to the new chiller plant, so as not to impact temperature and humidity in patient care areas. As such, EEI created step-by-step procedures for each building to be converted including a dry run of the conversion process prior to the actual cutover. EEI was designated as the conversion team leader responsible for coordinating multiple contractors and ensuring minimal impact to the OSU patients.