Jon Ross of Smith Seckman Reid responded to questions about both business and engineering aspects of working in a COVID-19 environment
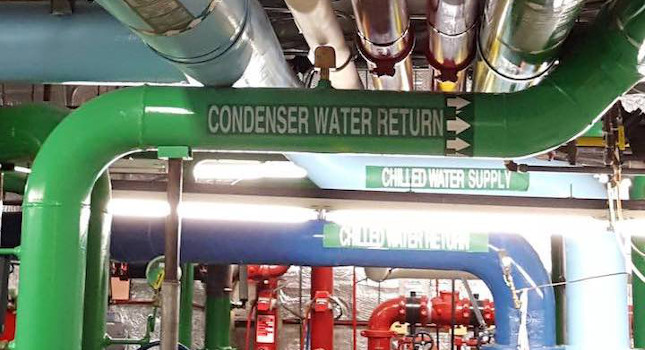
Jon Ross, senior principal at Smith Seckman Reid Inc., virtually answered a host of questions posed by Consulting-Specifying Engineer. Read on for advice and insights on the business of engineering and on technical engineering aspects.
Business aspects of COVID-19
How has your staff/team adjusted to the new work-from-home environment? What tips or suggestions do you have to help other firms remain connected while working remotely?
Jon Ross: Our colleagues had one to one and a half weeks from the time we announced we were going to work from home to being set up and working from home. They have adjusted quite well. Communication is key and we have all quickly learned to use the multiple virtual platforms for calls and meetings. We have encouraged video to better maintain connection between our colleagues.
We have intentionally increased meetings to multiple times a week to stay connected, whether senior leaders meeting daily, departments three times a week and offices one to two times a week having “all in” calls. Our project managers are being intentional about weekly project meetings and communication. We set up a community social board on Yammer and have daily discussion topics, many of which have little to do with work but keep our colleagues connected. One activity was a competition to see who had the best work space setup at home, which solicited a lot of discussion and friendly competition. Some managers have had virtual lunches with their teams while other groups have had virtual cocktail hours. There has been a lot of creativity in finding ways to connect remotely.
Just as important has been communication from leadership. We have sent emails from our CEO almost weekly to address issues and decisions that have been made. We have had multiple companywide video calls where our CEO shared updates of what is going on across the firm and took the time to answer questions from our colleagues. In addition, all of our leadership have made a priority to call multiple colleagues each day to check in, see how they are doing and see if there is anything they need.
Using technology has been critical to ensure that we get our work done, connect with our clients and continue to provide them an exceptional experience. It has been just as important to use it to connect socially with colleagues and clients to stay connected relationally.
Is your firm conducting any travel to visit clients or projects? If so, what types of projects are you working on?
Jon Ross: Most of our clients have restricted access to their facilities to some extent and our travel is down to a minimum. For our health care clients, our design meetings are mostly virtual meetings and we are only traveling to sites to support our clients with system issues or conduct fieldwork for projects. Many of our industrial clients are moving forward with projects and we have colleagues visiting and working in their plants to keep projects moving forward. Where our commissioning group has active projects, they are traveling to jobsites to do their work to help open new facilities, which include hospitals and stadiums. Our transportation group is staying busy and on jobsites as they are outside and keeping social distance is fairly easy.
What engineering or technical aspects of the job are now being done remotely?
Jon Ross: Many of our projects in the design phase are continuing, and almost all design meetings are being held remotely through virtual meetings. In one instance a client needed us on-site to resolve a system issue. We sent a person who then worked with staff remotely, showing them the site issues in a video chat to gather the information needed to resolve the issue. We had a hospital client that was ready for commissioning the controls system, but the site was restricted. Our commissioning agent got remote access to the controls server and was able to see the controls screen as they operated the system, allowing him to commission the system remotely.
What supply chain issues are you experiencing? Is your firm dealing with any challenges with materials or products from manufacturers or suppliers?
Jon Ross: Several construction sites have had trouble getting sufficient personal protective equipment for the workers and thermometers for checking workers as they entered the site. Some products sourced from China, such as lighting fixtures and lighting controls, have been delayed. Another project has had furniture delayed because the factory converted assembly lines to manufacture hospital patient beds. Deliveries of certain types of fiber optic cabling is experiencing significant delays because most of Corning’s glass manufacturing plants are in China and their Wuhan plant was shut down.
Do you expect to see pent-up demand hit once shelter-in-place restrictions have been lifted? How do you think business will trend three to six months after?
Jon Ross: Over the next six months, we expect the return of business activity to be mixed. There is no doubt that our health care clients will have a significant surge of business with elective surgeries that have been suspended. With the return of that stream of revenue we expect those projects that were put on hold will likely start up again. Our industrial clients have not slowed so they will continue business as usual. Along with health care and industrial, we expect federal work and infrastructure work to resume or continue, but many others may be slower to return.
What financial implications do you think this will have on the engineering industry as a whole?
Jon Ross: It is evident already that certain markets have been hit harder than others and the economy as a whole has slowed down. Our forecasts show the engineering industry will see a reduction in revenues this year of 10% to 15% on average. It is expected that 2021 will, at best, be flat with no growth as clients are focused on addressing the COVID-19 issues and maintaining their businesses, and not on potential projects for future growth. With the uncertainty of the total impact on the economy, it is expected some clients will be slow to commit to new projects until the future is clearer.
Engineering aspects of COVID-19
Have building owners or clients approached you to assist with changes or updates to their building to help protect against COVID-19? What services can you offer?
Jon Ross: We have had several requests from our health care clients to help accommodate the potential surge in COVID-19 patients. In one case, we designed the build out of shell space as a COVID-19 patient wing. Other clients have asked for assistance in modifying systems in existing patient areas for the same purpose. We helped one client repurpose a building to serve as an alternative care facility to take less acute patients and make room for COVID-19 patients in the hospital.
We consulted with many clients regarding their HVAC systems about improving filtration, changing air handling unit operation to 100% exhaust to eliminate recirculating air, and others on how to make spaces negative pressure to contain the virus. We have also worked with clients assessing their oxygen systems to determine how many ventilators the distribution lines in patient areas would support so they would know ahead of time any limitations they might have in serving a surge of patients.
For hospitals and health care facilities, do you anticipate further demand for specialty or pressurized environments?
Jon Ross: Many of our clients are wanting flexibility that gives them the ability for a simpler conversion to “pandemic mode” in patient care areas. Clients are interested in having HVAC systems for patient areas that can be switched to economizer or 100% outside air with all air exhausted in a surge situation so there is no recirculation of the air in the patient area. Some hospitals utilize waterside economizer systems in lieu of airside economizer. In this instance, the AHU ductwork and coils aren’t sized for 100% outside air, which makes it costly to modify an existing system to 100% outside air and exhaust air operation. Where this isn’t feasible, clients often want to increase the filtration to HEPA filters to minimize recirculation of contaminants. Clients are already talking about designing hybrid solutions for new bed towers where a portion of the building operates on waterside economizer and a portion will be operated on airside economizer to be able to convert some systems and areas to an isolation suite.
As we go forward with the design of new health care facilities, we expect clients will want these kinds of strategies and more to be incorporated into new facilities to prepare them for future pandemic type surges.
What test-and-balance or air balancing challenges have you encountered? What unique challenges are you solving?
Jon Ross: Many clients are wanting to switch AHU systems from recirculating return air to 100% outside air using their economizer operation mode to create pseudo isolation suites. This has been feasible in the spring, but the AHU systems weren’t sized for 100% outside air operation in the summer months, which are quickly approaching. We’ve had to replace cooling coils on some AHUs to enable them to dehumidify 100% outside air. Additionally, some facilities have created pseudo-isolation spaces with field-manufactured shrouds surrounding the patient’s head and torso. The shroud’s frame includes an exhaust intake ducted to a HEPA fan-filter unit within the room.
From an engineering standpoint, what other markets or building sectors do you anticipate will grow due to the changes occurring due to the coronavirus? Is there a new engineering sector you plan to focus on to meet these needs?
Jon Ross: We believe that health care will evolve but will continue to remain strong and grow. With the realization of how many of our products, medicines and supplies are manufactured overseas and how fragile the supply chain has proven it can be, we believe there could be growth in the industrial markets as well, bringing some of the manufacturing back to America. We are in both sectors and will continue to focus on them. During this time, we have all depended even more on technology to keep business moving and is making us all realize new ways to conduct business. Technology consulting with clients to help them integrate innovative systems should be in demand.
The coronavirus has required several facility managers to remotely control all aspects of their building systems (lighting, HVAC, etc.). What building automation or controls projects are you working on to meet these needs? How will this impact future design?
Jon Ross: The virus has pushed the facility and information technology teams to realize the need to “open up” their network for access to the building automation system by trusted employees and partners. This is a major step, as it allowed consultants to respond to client needs very quickly and troubleshoot system issues live, without a delay. Our clients have seen that several HVAC-related activities, such as commissioning and BAS graphics and database editing, can be successfully accomplished remotely and can actually lead to cost savings for the client. This has also shown some of our clients the benefit of monitoring-based commissioning as a means to help facilities maintain their building and keep things working per design requirement.
We believe that future designs will be required to engage the client’s IT department in terms of setting and securing the project environment for remote access and team collaboration. It will also have an emphasis on system wide BAS connectivity, dashboards and facility technology training.
What might other engineers/building professionals need to know when tackling COVID-19 projects?
Jon Ross: It is important to stay up to date on the latest Centers for Disease Control and Prevention guidance and understanding of the ways the virus is transmitted along with the various system design strategies that have been used to reduce the risk of the spread of the virus to other patients and care givers. With that, helping your clients know the options they have and the benefits of each so they can make the best decisions for the system approach that will meet their anticipated needs.
When a surge is projected and clients need to create COVID-19 patient areas, time is of the essence to make the patient care spaces ready and available. In our experience, the projects proceed in a design-build fashion regardless of the contractual arrangement. Design has to happen on a critical path with equipment often approved and ordered before the design is complete. Often many specifics get figured out in the field among the trusted partners.