Replacement of building automation systems can follow the process and precision of medical surgery
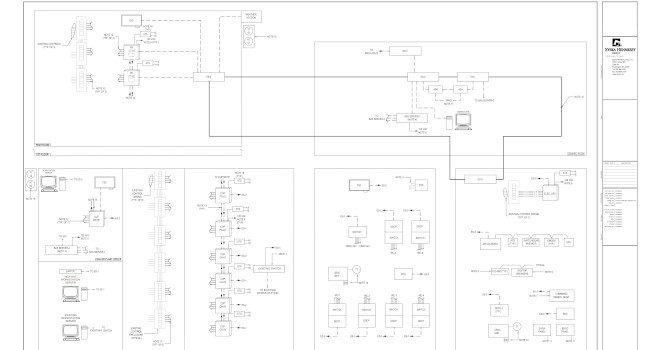
Learning Objectives
- Understand the impact of a building facility team’s vision on a building automation system replacement.
- Learn about tools that can be used to evaluate potential vendors for a BAS replacement.
- Know the techniques in preparing for the replacement of a BAS controller in a critical space.
A building owner or facility team may be interested in fully replacing the facility’s building automation system, but the engineering consultants and owner have concerns and fears surrounding potential complete facility shutdowns or interruptions of critical processes. A surgical BAS replacement can help allay these concerns and keep a facility operational while the automation infrastructure is modernized.
Similar to a delicate organ transplant, a BAS replacement requires a surgical level of precision to be successful. Facilitating the transition from an outdated, problematic system to a modern and sophisticated system while managing (or even eliminating) downtime of the controlled equipment should be the goal.
Here are some design considerations and approaches that can be used to support the next BAS replacement.
1. Vision for the building automation system
Before planning, it is essential to determine the overall vision for the facility and commit to this vision. What long-term goals do the stakeholders have for the facility? What is the current culture and/or mindset as it pertains to energy management and maintenance? What is the current culture surrounding information technology and cybersecurity?
Similar to how an organ replacement can fail if habits of misuse aren’t supplanted by healthy patterns of behavior, poor maintenance and management can sabotage even the most advanced and skillful BAS installations and replacements. Vision should begin with an honest assessment of the present before looking to the future.
It is estimated that approximately 40% of a commercial building’s energy usage comes from its HVAC system. Currently, the United States has a goal of reaching net zero carbon emissions by 2050. A BAS replacement in and of itself will not lead to achieving higher efficiencies.
That said, synergy does exist between better energy management and BAS replacement upgrades. Newer hardware with IP connectivity allows for interfacing with more data points using the “internet of things,” which, in turn, creates opportunities for more precise monitoring and control. Properly programmed analytics and fault detection diagnostics also help steer a BAS toward improving and maintaining energy metrics. The vision of a facility should not stop at avoiding penalties within the next five years, but for decades to come.
Embracing standards makes planning out the vision for the facility easier over time. If these standards are functions of expected business outcomes and key performance indicators, then they make future installations, upgrades or optimization opportunities seamless, regardless of which BAS vendor is chosen to execute the work. Information on how to get started on these efforts is readily available.
For example, after evaluating lessons learned from the existing installation (with input from in-house engineers), consider how the team will incorporate opportunities to improve upon future graphics that will make training next year’s operator easier and steer the organization closer to the goals set.
Many patients perform extensive research on the characteristics of the surgeon set to orchestrate their procedure. This mindset should also be applied when gauging a company’s ability to perform a BAS replacement. The evaluation process should dig deep into details such as: How readily available is the new hardware the company supports? What are the average lead times for supervisory controllers? How many vendors locally and abroad support the product? What is the size and longevity of the company in question to facilitate the BAS replacement? Pay close attention to the operating system requirements of more modern BAS hardware as well as server requirements.
An insurance commercial comes to mind where the doctor approaches a patient sitting on a hospital bed and asks, “Are you nervous?” The patient shakingly replies, “Yeah.” The doctor then replies, “Me too. Good luck out there,” and pats the patient on the shoulder.
To avoid this kind of scenario, as part of the project bid, a facility owner should request references to prior projects with similar or greater complexities and scope. Keep in mind that a surgical replacement for a commercial office building comes with a very different set of challenges and consequences than one for a data center or hospital.
Another key item to consider when documenting the present status of the facility is critical spaces or processes served by legacy control systems. A detailed report by the facility management team should include the exact location of those spaces, schedules of occupation and any special equipment required to heat, cool or maintain pressure in those spaces should the control system be inactive. The contingencies within this report should be revisited every time changes are made to these critical spaces. Where redundancy exists with cold standby (N+1) or hot standby (all equipment running), rotations and failure scenarios should either be part of a maintenance program, or their functions should be witnessed from the existing BAS in automatic mode.
The vision should also encompass the expected involvement of a facility’s IT department. This would include provisions for cybersecurity screening of the installing contractor’s current product line as well as its corporate cybersecurity standards. The IT company’s involvement should also aim for coordination with any future vendors so that a new building automation server can be installed and set up alongside the existing legacy equipment server before any new controllers are installed. A separate network for the operational technology devices should be created and internet protocol addresses should also be prepared in advance.
As part of the standard, supervisory and terminal unit controllers should be expected to be preprogrammed before arrival on-site. An opportunity may exist to have programming updated to the latest ASHRAE Guideline 36: High Performance Sequences of Operation for HVAC Systems. Graphics and simulation bench-test reports for controllers set to replace those serving critical processes should be provided for review by the operations team.

2. The BAS checkup
Universally, before a surgical procedure, a series of checkups and evaluations are required to understand the overall health of an individual and subsequently decrease complicating factors that could negatively impact the effectiveness of surgery. Similarly, the overall health and condition of the BAS should be assessed to document and consider correction to issues that could cause more harm than good for the new system.
Safety: Safety should be the No. 1 priority when evaluating a site for a BAS replacement. Do sensor cables exist in the same troughs or conduits as high-voltage wiring? What is the current condition of the control panel, starter and variable speed drive enclosure real estate? These questions must be addressed: Electrical hazards cause 30,000 non-fatal shock incidents and 1,000 deaths each year among the U.S. workforce alone.
From the consultant’s perspective, an opportunity exists to have hazardous panels replaced in alignment with a building standard that formalizes performance expectations and protects operating personnel from bodily harm. This goes beyond a typical “reuse existing” design keynote and should be part of a due diligence walkthrough.
As-built documentation: Poor as-built documentation can serve as a barrier to the successful execution of a surgical BAS replacement. Which control panels serving critical equipment have their dedicated power sources? Which ones have redundant power sources? Do sensors exist that are broadcast across the automation network? If so, would taking their associated panels down for a replacement create a ripple effect of issues for other equipment that must remain in operation? What are the current sequences in place?
Inaccurate as-builts make these questions difficult to answer and can create unanticipated change orders. It is not uncommon to find the answers to key questions on as-builts taped to the interior door of an existing panel enclosure.
Stability: The condition of the existing instrumentation made available to a surgeon is of paramount importance. The consultant’s approach to using either existing sensors, existing cabling or some combination of the two, must be taken very seriously. In addition to probable deterioration of the incumbent equipment due to age, legacy BAS installations tend to come with legacy sensors, some of which have antiquated control signals not used by modern control systems. Some additional items to take into account:
- The verification of current wiring integrity (Is solid core wiring in place for sensors?).
- Will the controlled equipment accept standard 0 to 10 volts direct current, 2 to 10 volts DC, 4 to 20 milliampere or 0 to 20 milliampere control signals?
- Integration in place: Some legacy systems use discontinued protocols that may require the use of a protocol conversion gateway to access. The same can be said for variable frequency drives.
- Do the current thermistor and/or resistance thermal device (RTDs) types conform to building standards?
These items can also be packaged as part of a proper due diligence report for review and remediation. Take for example steam boiler burner controls. Some come with modulating actuators that require a 0 to 135 Ω control input to vary the burner firing rate. Typical direct digital controllers do not come with this feature, so a converting module may be required or complete replacement of the actuator should the project budget allow.
3. Building automation system prep
The upkeep and environment of an operating room are set before a surgeon’s arrival. With all critical spaces properly identified and contingencies prepared, a sample schedule should be put together in Gantt format for reference as part of a BAS replacement plan. This should include sections for start times, anticipated downtime and any coordination required with the occupants of the space or those affected by its downtime. This allows the facility personnel to be prepared for weekend work or the triggering of the use of process control contingencies outlined above.
Where applicable, standard documentation should have sections allocated to recording the conditions of the room or process (temperature, pressure, humidity, valve positions, damper positions, etc.) before any work commences. This will provide a baseline for comparison post-replacement.
4. BAS replacement
The BAS replacement process is a very delicate one and requires a peak level of focus. The vendor performing the work must be given the room to operate with minimal interruptions. If there is a service contract in place and other equipment requires attention, a separate technician should be called on to address issues outside of the replacement scope.
Complications during any procedure are a reality that must be accepted and a good technician knows how to communicate when these situations arise. There are certain existing issues that would only be discovered while in the middle of the actual process and some contingencies — no matter how well-thought-out — are not enough to correct them. Dialogue between the technician executing the work and the personnel facilitating it will then cover which matters are critical and must be addressed immediately and which are not.
Upon controller replacement, the point-to-point checkout must be thorough. This process should encompass testing of the instrumentation as well as the sequences (both at the equipment level and the integrated automation level). Once complete, it is up to the facility to decide whether to involve third-party commissioning. Keep in mind that a vendor-agnostic approach to validating the operation of the new BAS hardware provides additional assurance that the surgical replacement was successful.
Updates of the as-built documentation should be verified and include updates to network topology. This information, along with the point-to-point checkout report and commissioning forms, should be filed for review, approval and future reference.
5. Follow-up and analytics
Post replacement, a follow-up should proceed in a fashion similar to a post-surgery checkup. If the new BAS platform has analytics and fault detection capabilities enabled, the activity of comparing performance against the building’s standards can become a continual process.
Some say that the BAS acts as the eyes, ears and hands of a facility. Regardless of the organ chosen for comparison, all can agree that proper functionality before and after a replacement is critical. Approaching a BAS replacement with a surgeon’s precision can make a procedure once surrounded by fear a process to be embraced with confidence.