The escalating cost of providing potable water in the United States is creating new urgency for owners of commercial, industrial, and institutional buildings to respond with greater engineered water efficiency.
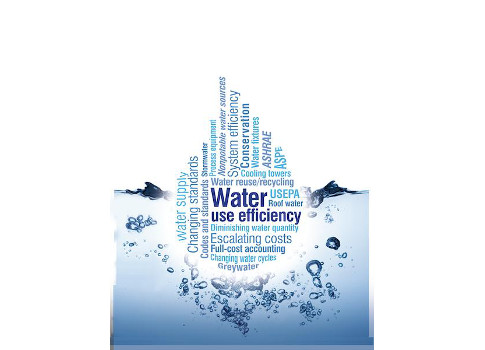
- Understand the true cost of water in the commercial building sector.
- Learn about ways to conserve and/or reuse water.
- Learn about water standards and how they are changing.
National surveys of the cost of public water supply utility rates show average annual rates of increase over the past 10 to 20 years as high as 8% per annum. According to an often-quoted survey of 100 U.S. cities whose findings were published in USA Today, rates of water/sewer utility cost increases from 2000 to 2012 average 7% per annum over that term with the greatest increases concentrated in the nation’s largest cities.
Proven techniques and technologies exist to design and retrofit for significant cost-justified water efficiency. Driven in part by the sustainable design movement, some strategies outpace existing regulations and codes. However, economic necessities, mainstreaming sustainable sensibilities, and the results of pilot testing of water reuse and recycling are combining to suggest that standards will soon catch up.
The rising cost of water
While other utility rates have generally tracked the Consumer Price Index, water and sewer costs have, in the past 30 years, increased at a much faster pace (see Figure 2). A web of interconnected reasons for the growth in water and sewer utility rates explains this phenomenon and suggests that the trend will continue (see sidebar, “Why is the cost of water rising?”). From the perspective of water’s status as a public good, some who monitor this issue suggest that the public has, perhaps reluctantly, accepted this cost phenomenon. Association of Metropolitan Water Agencies executive director Diane VanDe Hei sees it a bit differently. Observing Seattle’s 2011 move to increase water rates by 25% over a 3-year period, she suggests that despite a depressed economy and significant anti-tax sentiment, the public will pay to ensure long-term access to water of the quality and quantity that they desire.
While this may be true, it should not be confused with an unwillingness to conserve water use. The significant distinction is which water uses we are willing to conserve. It appears that there is no strong inclination to conserve water for uses considered essential to health. Thus, at the household level, the most likely accommodation to a call for conservation is in restricted water use for landscape or optional cleaning, such as car washing. A secondary interest would show itself as willingness to participate in subsidy programs for showerhead water restrictions or more efficient toilets—activities that still allow for the basic water-using activity of a household, but with more efficient resource use.
Meanwhile, studies establish that commercial /industrial/institutional entities do respond to increases in the price of water through reduced use of water supporting non-health-essential functions. This conservation response occurs across the spectrum of utility price points, not just in locations where the cost of water is most expensive; it is a reaction to change in price more than to absolute price. These modified processes and practices differ from those of the residential sphere, which tend to respond episodically to drought conditions rather than by instituting fundamental ways of reducing water use. In the commercial/industrial/institutional setting it is possible to more than offset cost increases with conservation.
Water use efficiency in code, building rating systems
In the past 20 years, water efficiency has been a less urgent cost issue, and thus codes and building rating systems have focused on enabling greater energy efficiency. Consequently, there has been measured and slow research to examine the real or perceived health risks associated with water reuse as part of creating a path for safe water reuse. The International Association of Plumbing and Mechanical Officials (IAPMO) has made significant updates to the uniform plumbing codes (UPC), including issuing the first Green Plumbing and Mechanical Code Supplement in 2012. However, the UPC covers only a fraction of the water usage in buildings, and many states and local governments have yet to adopt the new code. Water use related to nonhuman consumption is only beginning to be addressed in the codes.
ASHRAE 191P: Standard for the Efficient Use of Water in Building, Site, and Mechanical Systems is a proposed standard that works to address water usage in buildings holistically. ASHRAE 191P is meant to be a minimum standard with high-performance water usage governed by ASHRAE 189.1: Standard for the Design of High Performance, Green Buildings. ASHRAE 191P governs:
- Site water usage
- Greywater
- Plumbing systems
- HVAC systems
- Appliances
- Process equipment
The standard is being developed in cooperation with the American Society of Plumbing Engineers (ASPE) and the U.S. Green Building Council. A first draft of the proposed standard was issued for public review in October 2012, and review comments are currently being incorporated into a second iteration.
LEED 2009 for Healthcare introduced prerequisites and credits for process loads, food service equipment, and cooling towers, as well as submetering water usage. This approach has been expanded in LEED v4 (November 2013 release). However, even with a gaining presence in the marketplace, it is estimated that approximately one-third of new commercial construction is designed to LEED standards.
The Living Building Challenge, a nascent program with three buildings that have achieved “living” status, works to press and inspire the design community to move beyond LEED. Comprehensive in its reach of issues, it calls for net-zero water buildings. Here, participating building owners work to use only water that can be captured on-site and to safely process and retain all of it on-site once that water is used. Stormwater also must be managed naturally and within the project site.
Regardless of efforts to advance regulation to allow for water reuse and recycling and of the progress of building rating systems to guide a more aggressive path, some contrary legislative anachronisms exist. Fifteen western states’ constitutions, statutes, and case law are tied to the prior appropriation doctrine, a mid-19th-century concept that does not recognize water rights as connected to land ownership, but to use (and prior use). Those who argue that these laws do not benefit contemporary needs reference recent case law that promises movement toward enhanced ability to manage water to better serve the region’s population and environmental protection needs.
Water use efficiency in new construction
The first priority in designing for water-efficient buildings is to do what is easiest and most cost-effective. Regardless of building type or geography, this priority is addressed through avoiding water use. Five universally cost-effective examples are:
- Reduce lawn size and select plants appropriate to their settings. This can be accomplished without sacrifice to the aesthetic or monetary value of the site.
- Attend to the fundamentals of building orientation and massing to reduce building energy demand. In so doing, these steps work to reduce the size and water use associated with building mechanical systems.
- Engineer building systems for energy efficiency; this will also reduce water use.
- Select the right equipment. Energy- and water-efficient equipment can be identified through a combination of relying on the U.S. EPA WaterSense and Energy start programs and through the design team’s own research. In this setting, equipment refers to water fixtures, landscape equipment, kitchen equipment, and scientific and medical equipment.
- Procure the right amount of equipment. Some building use lends itself well to shared locations for some equipment with the consequence being reduced water and energy use (and capital investment). Meter and automate water use on the desired schedule and as programmed to meet specific circumstances.
The second priority is to use second generation and inferior (nonpotable) quality water. Strategies include:
- Access the availability and cost of reuse water sources, looking for reduced cost combined with appropriate quality and quantity to support project reuse opportunities. Alternative water sources can be found both in and outside of the building. These include cooling coil condensate waste water, desalinated water, equipment/system wastewater, fire pump testing water, foundation drain water, groundwater, municipal treatment wastewater, roof water, surface water, and stormwater.
- Reuse water within the building project. This dictates water quality and quantity (including schedule of quantity over a year) that matches between donor water and use that can employ this water. Building water-consuming uses that can easily reuse water range from the kitchen and laundry room to the mechanical systems and central plant. By way of strategy, the best success comes with working to first match large sources and large water-consuming activity.
- Identify reuse water opportunities outside of the building project that can consume the building project’s wastewater. Secure those opportunities rather than releasing good quality water to the municipal sewer system.
Recycling water is a third priority because it implies water treatment, using more energy and chemicals than water reuse. Site landscape and central plants are locations that offer great opportunity to use recycled water. However, some recycling activity is more challenged to gain needed approvals than is water reuse. For example, using treated greywater for toilets typically comes first to mind when one thinks of a use for recycled water within a building. This is an excellent response when a site has no or constrained access to public water and sewer utilities. However, in the majority of settings the viability of this greywater reuse is undermined by regulatory hurdles and/or is cost prohibitive compared to other water recycling options.
Water use efficiencies in existing buildings
Water conservation in existing buildings can be compared with energy conservation: opportunities range from low-hanging fruit (affordable investments with short payback terms) to complex, expensive investments with worthwhile paybacks over a longer timeframe. In each setting, building owners establishes their desires in terms of paybacks, total investment budget, and innovation.
The first priority for water conservation in existing buildings is to institute the least expensive water conservation measures: avoided water use. Changed landscape management and facility maintenance regimens can save water, energy, and maintenance labor costs. Though not undertaken with the objective of water use reduction, a regular schedule of recommissioning is similarly attractive: saving water, energy, and building maintenance labor costs.
The second priority is to make existing systems and equipment more water efficient. This is accomplished through two approaches:
- An inventory of mechanical systems and water-consuming equipment in the building to assess proper use, condition, and utility.
- Exploration of opportunity to modify and/or replace elements of mechanical systems and water-consuming equipment to introduce or expand on facility water reuse and recycling.
The results of this effort will recommend a combination of improved facility operations and a schedule that addresses a combination of equipment replacements (in-kind and upgrade to a more water-efficient alternative) and cost-effective means of introducing or expanding water reuse and recycling.
Metrics: The potential for water use reduction in the commercial/industrial/institutional sector
While techniques for reducing water use are well established, the metrics and rigor of chronicling their outcome lag. Ideally, water use reduction experiences would be described by quantity of water volume reduction in the categories that are likely to be the three largest factors by volume:
- Total water use for irrigation (potable and reused/recycled water metrics)
- Building reuse/recycling of water exclusive of cooling towers or central plant
- Reuse of water in cooling tower or central plant.
Following is an introduction to three sources of information that both generalize and provide desired, specific analysis of water use reduction potentials for building types found in the commercial sector.
First, federal agencies operate under several mandates that address sustainability, including EO 13423 and 13123, which require agencies to reduce water consumption intensity (measured as gal/sq ft) by 2% annually through FY 2015 or 16% by the end of FY 2015 (2007 baseline). EO 13423 also mandates a schedule of water audits. EO 13514 expands on the earlier guidance in dictating 26% water consumption intensity reduction by FY 2020 (using FY 2007 baseline).
The Dept. of Energy’s (DOE) Federal Energy Management Program, Office of Energy Efficiency and Renewable Energy is the repository for all agency data. It characterizes the primary building use of these agencies, allowing the owners of certain types of commercial buildings to see what the federal government accomplished between 2007 and 2012 in reducing water use in these same building types:
Each of the 17 federal labs (DOE) offers detailed information about its water use reduction strategies and accomplishments on its websites. Two examples:
- The National Renewable Energy Lab (NREL) FY2013 Site Sustainably Plan details significant water consumption use intensity reduction on that campus. It chronicles that the campus reduced potable water use intensity by 30% between FY 2007 and FY 2012. To accomplish this, NREL modified its design standards and operational procedures to promote efficient use of potable water, created operational constraints on all once-through cooling devices, installed comprehensive metering, established a regular program of water audits linked to capital planning, installed smart irrigation systems to support the limited lawn area that it does irrigate in order to aid the establishment of its plants, and replaced its gas scrubber with one that uses no water (decommissioned scrubber used 2.2 million gal/year).
- The Pacific Northwest National Lab (PNNL) reduced its metered facilities from a water consumption use intensity (gal/sq ft) of 77 in 2007 to 31 in 2012. To accomplish this, it installed a comprehensive system of meters, replaced bathroom fixtures, installed flow restrictor aerators in lavatory sinks, established a regular program of water audits, and instituted a system for reducing landscape water use.
Second, Waste Not, Want Not: The Potential for Urban Water Conservation in California is the Pacific Institute’s 2003 comprehensive modeling of water conservation potential by Standard Industry Codes (SIC). Examining the building use activity associated with select codes, here is a bottom-up analysis of cost-effective water use reduction. Careful to qualify that the analysis relied on the best available—though imperfect—data, a range of conservation potentials for buildings (including landscapes) in the State of California are shown:
Finally, popular and design industry press sources and the Internet provide valuable information about project water use accomplishments and strategies. A sampling of informative presentations about water conservation in existing commercial/industrial/institutional facilities includes:
- MicroSemi UPSD Inc., a semiconductor device manufacturer, reduced its water use by 30%.
- Intel Corp., a semiconductor chip maker corporation, has made a corporate commitment to water use reduction that shows itself across many Intel campuses.
- Stanford Hospital & Clinics, a regional scale comprehensive health care provider, saved more than 12 million gal/year by upgrading its sterile processing equipment.
- Water Sense: an EPA Partnership Program is a federal program that provides the public with information and education about water efficiency. For a collection of case studies, visit the website.
Willa Kuh is Affiliated Engineers’ director of planning. She has expertise in campus projects with an emphasis on resource planning, assisting clients in their development of facility master plans, strategic energy plans, sustainability plans, and climate mitigation plans. Kuh is a planner for the UW Health at the American Center project. Fred Betz is a senior sustainable systems analyst with Affiliated Engineers. With a doctorate in building performance and diagnostics from Carnegie Mellon University, he specializes in advanced building systems integration, energy and other resource simulation and planning, renewable energy and power generation, and controls and diagnostics. He is the lead energy and water analyst for the UW Health at the American Center project.