High-noise manufacturing environments are already difficult places to communicate, but COVID-19 and social distancing make it even harder. Learn how to overcome this challenge.
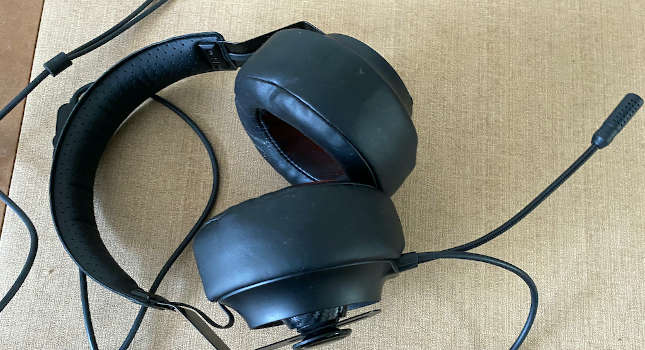
Communication in manufacturing can be a challenge even under normal circumstances. Noise from machinery and distance between workstations creates barriers that can prevent even normal conversation between employees from occurring. Add in new social distancing guidelines and a real dilemma to productivity and employee engagement must be faced. If these issues can be overcome, manufacturing companies have the potential to develop real competitive advantages in the marketplace. Plant employees, especially those on the manufacturing floor, are a great source for new ideas when it comes to standardizing operations and continuously improving processes. These changes can result in cost efficiencies, product enhancements and improvements in time to market. Any way to improve communication will have a great impact on team morale and productivity, resulting in better bottom-line results for the company.
Manufacturing noise levels
Sound from manufacturing processes, machinery and equipment all have the potential to produce high noise levels that can adversely affect communication on the manufacturing floor. In addition to employees sharing information and ideas with each other, this noise creates a safety issue if it makes safety alerts hard to hear. Forklifts and other vehicles are commonly used on manufacturing floors. If an employee can’t hear the sound of a vehicle approaching or backing up, it could result in a serious injury. Other alarms and warnings also are at risk of not being heard, which raises the concern of every environmental health and safety (EHS) manager in industrial settings. In addition, high noise can present a potential health risk.
According to the U.S. Department of Health & Human Services, prolonged and repeated exposure to high noise may cause hearing problems if precautions are not taken. Hearing protection is a must when on the manufacturing floor since employee health is the most important factor to consider. However, it does present another obstacle to hearing what a fellow employee is saying and therefore impacts communication in the workplace.
Workstation distance
In manufacturing facilities, most workstations are designed for minimal wasted motion and purposeful action. Workstation set-ups focus on safety, ergonomics, and the efficiency of getting parts and having the right tools available to get the job done. While most processes will have tasks done as close together as possible in order to stay efficient and increase productivity, distance is still needed since machines and employees require space to get the necessary work completed effectively.
Social distancing in manufacturing
Manufacturing is a critical part of the United States supply chain. Following a CDC statement, many industries are considered essential and have remained open during the COVID-19 pandemic. While the work continues, many changes have occurred to help keep workers safe in the workplace. OSHA, following the CDC’s recommendations to stop the spread of the virus, has recommended guidance for manufacturing facilities to take in order to protect employees.
When it comes to creating distance to stop the spread of COVID-19, OSHA recommends staying 6 feet apart at all times, repositioning workstations and installing barriers between employees, wearing personal protective equipment (PPE) including masks, and staggering work schedules to limit contact with others. All these steps are important and must be followed, but they create additional challenges to employees being able to communicate clearly and effectively with one another.
Headset communication systems
An effective way to help employees overcome noise, distance and other barriers to communication is to provide workers with staff communication systems. These systems consist primarily of headsets and transceivers and allow for either one- or two-way communication. Headphones and microphones have increased value when it comes to communication since masks are now hiding facial expressions, lip reading and voice communication. In the past, these nonverbal communication cues would help employees give and receive messages to one another.
Delivering a clear message
Communication in a manufacturing environment has always been a challenge. Noise from machinery and distance between workstations make it difficult for employees to speak and hear each other. COVID-19 has added additional obstacles through social distancing protocols and PPE requirements. In order to promote communication and get the most out of employees in terms of productivity, new idea generation and morale, plant managers should provide the resources to overcome these issues and make communication easier in the most efficient way possible.
For more information, please visit Plant-Tours.com