Leaders from WSP USA reply to questions about how they’re addressing engineering challenges in direct response to COVID-19
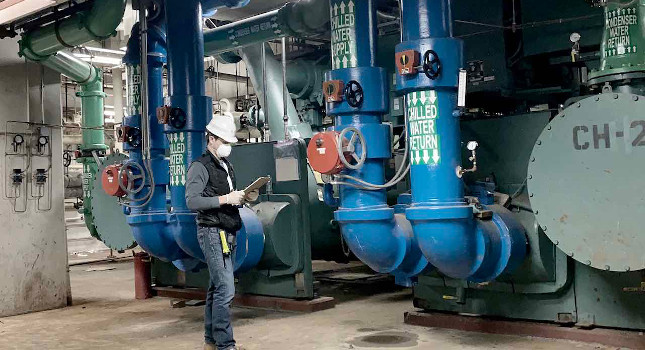
WSP USA leaders provided responses to an email Q&A on various ways COVID-19 is changing how they approach engineering challenges. Respondents include:
- Lou Cornell, PE, president and chief executive officer, WSP USA, Orange, Calif.
- Rick Rome, PE, chief operating officer, property & buildings, WSP USA, Dallas
Have building owners or clients approached you to assist with changes or updates to their building to help protect against COVID-19? What services can you offer?
Lou Cornell: We are advising clients on things like how to implement more outside air and increase air change rates and how smart building systems can help building owners better manage their spaces and create a safer environment for users. There is also an increased interest in remote building monitoring and management. Other considerations include things like automatic doors and contactless security, as well as motion-sensing for plumbing and light fixtures.
Our teams are also looking at what we can borrow from our health care and containment lab engineering expertise to advise clients in the commercial, residential and hospitality spaces, as well as others. We are working with clients to identify what technologies used in hospitals could be adapted for other settings, in a way that is cost competitive and provides a level of comfort without intruding on people’s lives.
In addition, our emergency response team has been contracted to manage complex disinfection in machinery-filled workspaces from midsized to a million square feet. We anticipate more of these projects as businesses prepare to reopen and need to manage contagion moving forward.
As an example, one day after two employees tested positive for COVID-19 at an essential processing and distribution center, WSP mobilized to perform a disinfection sweep. It was started Saturday and completed by midnight Sunday, allowing the facility to reopen Monday morning. Disinfection of the three-floor,1 million-square-foot building was performed and inspected by a WSP-certified industrial hygienist to ensure that the specified procedures were followed. A final report documenting activities and waste disposal was prepared.
What test-and-balance or air balancing challenges have you encountered? What unique challenges are you solving?
Rick Rome: Our air balancing technicians perform routine critical space testing for a large number of hospitals in the Maryland, Washington, D.C., and Virginia area. These critical space testing services focus on spaces such as operating rooms, immunocompromised patient rooms and airborne infectious isolation rooms, which must be tested regularly for proper airflow exchange rates and pressure differential to adjacent spaces. These testing services have been in high demand as health care systems verify and adjust the HVAC systems to provide a safe environment for their patients and staff.
One of the more challenging problems that we have faced is the need for negative pressure operating rooms for COVID-19 patients, which technically are not allowable by code. We have helped our hospital clients create negative pressure vestibules adjacent to the surgery space that are negative in pressure with respect to the corridor, but still allow the operating room to maintain positive pressure to the vestibule, thus protecting adjacent sterile areas. In general, our work has focused on HVAC adjustments to ensure proper and constant pressure relationships for those spaces and ultimately, protection of the patients and health care workers.
One of the unique challenges we have encountered is adapting and adjusting existing HVAC systems to fully protect patients and staff. Many HVAC systems are designed to operate in an economizer mode, saving energy by using 100% relief air and 100% outdoor air when outdoor air conditions permit. Our hospital clients have used this operational mode to create negative pressure floors and suites within their facilities. However, as outdoor temperatures and humidity increase the system cooling capacity will not be adequate to accommodate this economizer mode. As a result, we are working with our clients by determining when the system will need to be converted back to return air and assisted with converting to HEPA filtration at the central air handling systems.
For hospitals and health care facilities, do you anticipate further demand for specialty or pressurized environments?
Rick Rome: We do expect the demand for specialty and pressurized environments to continue and are working to assist hospitals with the creation of areas specifically to treat patients who test positive for COVID-19. It’s important to remember that before acting, medical facilities should make sure that the areas they chose to covert into temporary intensive care units can address all key attributes. In addition to positively pressurized patient rooms with higher air change rates, they should be able to provide additional power and medical gas capacity and not overlook the need for support spaces that can handle a more intense nurse-to-patient ratio.
On the other hand, not all of these attributes may be required to handle surge capacity. Additional medical gases and power for more ventilators are a must and accommodations for isolation of patients and ICU nursing to patient ratios are also key. But in some circumstances, positively pressurized patient rooms with higher air change rates may not be desirable; in fact, the ability to quickly adapt rooms to negative pressure, similar to airborne infection isolation rooms, may be more important.
We can learn a lot from what we have done so far, but it’s important to remember that there is no “cookie cutter” design. Meeting with medical personnel early in the conversion process and use their knowledge of their facility and their patients is the best way to determine the optimal solution for their particular situation.
The coronavirus has required several facility managers to remotely control all aspects of their building systems (lighting, HVAC, etc.). What building automation or controls projects are you working on to meet these needs? How will this impact future design?
Rick Rome: We are seeing a rise in interest in smart building systems as a result of the pandemic. What some building owners have previously seen as bells and whistles that don’t impact the bottom line are suddenly critical. In the near term, this includes the ability to control and monitor building health remotely, but there are further positive implications of these systems as people begin returning to their buildings work.
For example, it’s very useful to be able to leverage building system data to let employees reserve desks (and notify them which ones are available to use in light of social distancing protocols); or to have sensors monitoring use of cafes or restrooms to inform cleaning schedules; or to be able to switch off HVAC and other systems on a floor that isn’t in use because a reduced workforce is in the office.
We expect increased interest in the design and operation of smart buildings systems to continue, as building owners and tenants work to protect a returning workforce and be better prepared should a similar situation arise in the future.
What might other engineers/building professionals need to know when tackling COVID-19 projects?
Lou Cornell: Many of us, and especially our field leaders and supervisors, have trained to work in potentially hazardous conditions. Using safety equipment has always been a part of our work, so engineers and building professionals are in a position to use the principals of our existing training and experience to safely execute actions that may be necessary in these times.
But even with that experience, we must remember that this extends farther and in new directions, than what most of us have ever dealt with before — especially our younger engineers who may not be as comfortable in these situations as veteran engineers and building professionals would be. Mentoring and teaching those who are less experienced is critical.