Philip Lyman, PhD—director of process simulation at CRB—discusses how a process model, at the right detail level and properly validated, can be an invaluable tool to compare alternatives and justify cost for manufacturing and manufacturing-related processes.
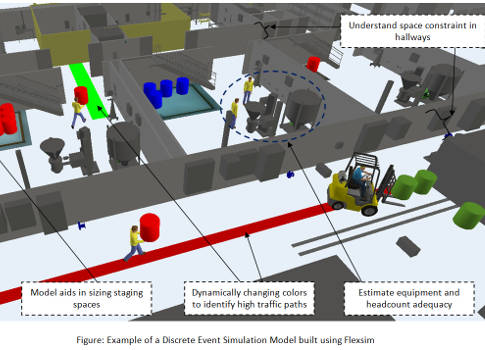
A process model is a computer representation of a real-world system or process. For our purposes, we are restricting the topic to models for manufacturing and manufacturing-related processes, such as batch documentation, material replenishment/warehousing, and quality-testing laboratories. The main purpose of the computer model is to act as a substitute (from a behavioral standpoint) for the real thing. It may be too expensive or disruptive to experiment on the real process; or, perhaps the real process does not yet exist and is still being designed. Regardless of the scenario, a computer model can perform experiments or "what-if" studies that can add to your understanding of the real-world system and identify and compare alternatives that improve the system in some way, usually to reduce costs or increase the throughput.
Another argument for using computer-based modeling is that the real-world system is often very complicated, involving many interactions between variables that may be unknown or poorly defined with significant variability that tends to hide the underlying relationships. A good model is a simplified version of the true system that captures the essential relationships while leaving out unimportant details. If variability exists and can be quantified, then this can be included in the model to provide a more realistic result.
Definitions
Simulation is sometimes used interchangeably with modeling, but really, simulation is the result of running a model. The model comes first; that model is then used to perform simulation studies. Typically, you are using a model to either reproduce a historical period (for validation purposes) or to extrapolate data to predict the future (for what-if studies). You may perform many simulations with a single model, exploring additional alternatives or replication with each simulation.
Benefits of simulation
With these definitions of process modeling and simulation, what benefits can we expect from this technology? I categorize the benefits according to the situation in which a model is developed and used:
Design phase—facility is being designed or will soon be designed. It’s best to start as early as possible in the design process. Changes to the design, prompted by simulation results, are more cheaply made early in the design.
Renovation—a facility exists already and needs to be improved in some way. Typical objectives are to increase throughput, reduce manufacturing costs, lower inventories, or some combination of these. Note that the improvements that come out of a study for an existing facility may or may not include equipment changes. Sometimes, improvements can be made simply by changing the operating procedures or product scheduling alone.
Design phase or new facility
Process modeling of a new design can provide the right number and size of necessary processing and supporting equipment. This is particularly valuable for equipment that is shared by multiple unit procedures such as CIP skids, utility system designs and powder bins and tablet totes in an OSD facility. The overall production process may have an equipment bottleneck; the model will identify the bottleneck and ensure that it does not constrain production to a value less than the business objectives for the facility. Also, the model will examine other potential bottlenecks. If their constraint is close to the desired bottleneck, then schedule disruptions or other variability may result in a constraint that is lower than the design, effectively substituting a more restrictive bottleneck for the desired one.
Changes occur frequently during the design process. Engineers find better alternatives, and management may change the product mix of volumes that the facility will be expected to make. In these instances, having a process model of the design is especially beneficial. The model can be used to evaluate the alternatives and ensure that the changes are cost-effective while maintaining the desired throughput. Staffing levels and shift schedules can also be compared with a model. This helps with cost justification of the design change.
Facility renovation
A model of an existing facility can provide the same benefits as a design model with two important differences. First, there is historical data that can be used to give a better model and to validate against the performance of the model. This helps to prevent process modeling errors and provides greater confidence in the model results. Secondly, the model is more likely to be used for operational decisions, such as production schedules and shift schedules. Equipment changes are still possible, but the scale of the possible changes may be lower if the facility footprint is fixed. Intermediate inventories may be fixed for the same reason, creating other problems for manufacturing. Models of existing facilities tend to be more realistic and detailed, which requires more engineering time to build, validate, and use the model.
Conclusion
A process model, at the right detail level and properly validated, is a valuable tool to compare alternatives and justify their cost. These benefits apply to new facilities during the design phase and to existing facilities that need renovation or operational changes. Further benefits accrue when each facility has an up-to-date model. Usually, good decisions must be made quickly, and this is only possible if the time and effort has been invested in a process model beforehand.
-Philip Lyman is director of process simulation at CRB’s Philadelphia office. This article originally appeared on www.crbusa.com. CRB is a CFE Media content partner.