Engineers should work to design the most efficient water heating system or boiler possible. Understanding the codes/standards is paramount, followed by knowledge of the key equipment functions of boilers and similar systems.
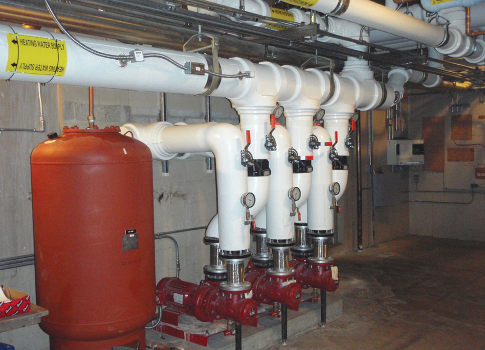
Learning objectives
- Learn about the components that make up hot water systems: boilers, pumps, and coils.
- Understand system control strategies for efficient system operation.
- Learn to maximize the efficiencies of these components.
Designing efficient systems of any kind requires consideration of the individual system component efficiencies as well as the overall system operation. In the case of hot water systems, the individual components are the boilers, pumps, and coils.
Boilers
The boiler is the primary energy-consuming piece of equipment in a hot water system. The costs associated with its energy use over the lifetime of the equipment will far outweigh the initial equipment cost. A careful comparison of the fuel-to-water efficiencies should be made as part of the equipment selection process and economic analysis. The fuel-to-water efficiency is a measure of the overall boiler efficiency that includes burner and heat exchanger performance as well as the thermal losses through the boiler casing. Minimum boiler efficiencies are required by the Dept. of Energy, energy standards such as ASHRAE Standard 90.1: Energy Standard for Buildings Except Low-Rise Residential Buildings, and state energy codes.
Boiler efficiencies vary with the type of boiler and operating parameters. Traditional noncondensing boilers have efficiencies in the 80% to 85% range. These boilers are designed to operate at vent temperatures above 127 F, which is the dewpoint of the combustion gases. This results in hot water system operating temperatures of 160 to 180 F supply and 135 to 140 F return to ensure that the return water temperature remains well above the combustion gas dewpoint. Operating this type of boiler below the combustion gas dewpoint will significantly shorten the life of the boiler. Noncondensing boilers are most efficient when they are firing in the 60% to 80% range. This makes them good candidates for base load or peak load operation.
Condensing boilers have efficiencies in the low- to mid-90s. The efficiency increase is primarily due to latent heat recovery from the combustion gases. This results in the boiler operating below the combustion gas dewpoint in the condensing range. As a result, hot water systems using condensing boilers have lower operating temperatures, 140 to 160 F supply, and 100 to 120 F return. Lower return water temperatures result in more latent heat recovery from the combustion gases and increased boiler efficiency. Condensing boilers are most efficient at lower firing ranges of 20% to 50% (see Figure 1). This makes them ideal for part-load conditions.
Due to the potential higher efficiencies, condensing boilers are seeing increased use. However, the traditional considerations employed in noncondensing systems must be revisited when using condensing technology. The first of these is turndown.
It is a widely held belief that the higher the turndown, the better. Let us compare a constant flow 5:1 turndown system to a 20:1 turndown system. In this example the system has a 1,800 MBH output boiler, a 90 gpm constant speed pump, and a 130 F hot water supply temperature. Ignoring losses, the boiler input must be equal to the output to the hot water system:
Q = mCpdT
Where Q is the boiler net output
Cp is the specific heat capacity of the fluid
dT is the temperature difference of the fluid (Ts-TR)
For water the equation simplifies to Q = (GPM)*500*dT
At full fire the temperature difference is 40 F, resulting in a return water temperature of 90 F (see Table 1) and a boiler efficiency of 94% (see Figure 1).
Using a 5:1 turndown, the system will operate at 20% of capacity with a temperature difference of 8 F and a resulting return water temperature of 122 F (see Table 1). Even though the temperature difference has decreased significantly, the boiler will continue to operate in the condensing range and can maintain a high efficiency at low fire (see Figure 1).
The 20:1 turndown system will operate at 5% of capacity with a temperature difference of 2 F and a return water temperature of 128 F (see Table 1), which is above the condensing temperature of the combustion gases. The result is a decrease in efficiency to 88% or less. The condensing boiler investment is now functioning like a noncondensing boiler. The turndown ratio is dependent upon the boiler capacity and its anticipated part loading and must be part of the overall system evaluation.
Boiler staging also needs to be evaluated. In heating plants with multiple noncondensing boilers, it is common to load the operating boiler(s) to upwards of 90% before bringing another boiler on line. This strategy attempts to minimize the amount of time the boilers are below their most efficient firing range. When applying condensing boilers, this thought process needs to change to take advantage of their excellent part-load efficiency. Operating multiple boilers at firing rates of 50% or less can result in an efficiency improvement of 4 to 8 points compared to the full fire efficiency, depending on the hot water return temperature (see Figure 1).
All boilers lose efficiency when they cycle on and off. This is due to heat being lost through the jacket, post-purge, ambient air flowing through the boiler after the boiler turns off, and pre-purge. The lost heat must be replaced in order for the boiler to reach its operating temperature. Frequent cycling results in increased energy consumption and lower overall efficiency. Short-cycling can be minimized by avoiding oversizing of the boiler and providing multiple small boilers in lieu of one large boiler. Purge cycles are still required for safety reasons as well as boiler and flue longevity.
Pumps
Pumping schemes for condensing boiler plants vary considerably from those of traditional noncondensing boiler plants that employ constant volume pumping or primary/secondary pumping. Unlike noncondensing boilers, primary variable flow pumping can be used with most condensing boilers. The recommended minimum flow through the boiler needs to be taken into consideration, but there are typically no minimum return water temperature requirements. The minimum flow bypass should be located toward the end of the distribution system. The pipe must be of adequate size for the required minimum flow rates to also avoid excessive pressure drops and increase the pumping energy required. This will maximize temperature losses and ensure adequate mixing before returning to the boiler plant. The bypass should be provided with a modulating control valve hardwired to the boiler plant controller. This will eliminate any control system delays that could occur when the valve is wired to another controller in the control system. The bypass valve should be controlled to maintain boiler minimum flow, as measured by a differential pressure sensor across the boiler, with a slight margin of safety to avoid nuisance tripping. Bypassing too much water will raise the return water temperature, which can adversely affect the boiler efficiency.
Thorough pressure drop calculations are required to evaluate the required pump head and optimize the piping system. A reasonable safety factor should be included only after this analysis. Oversized pumps are not desirable, from an efficiency standpoint, in a variable flow application. Pumps should be selected to maximize their efficiency. Electronically commutated motor (ECM) technology makes it possible to economically provide variable pumping for systems that require less than 5 hp pump motors.
Coils
Selecting coils for new systems is relatively straightforward. The water temperature difference across the coil should match that of the boiler. In moderate climates where the heating loads are low, this occasionally may not be possible while maintaining turbulent flow through the coil. When that is the case, the coil should be selected with a leaving hot water temperature at full load that results in the boiler operating in the condensing range. Both air and water pressure drop through the coil should be minimized without oversizing the coil. The air side leaving temperature should be less than 90 F to prevent stratification in the occupied space.
Retrofit applications may not require replacement of the existing heating coils just because the hot water supply temperature is lower. It is not unusual for the existing coils to be oversized, especially for zone level reheat. The existing heating coil performance at the new hot water supply temperature will need to be checked. The first example is an existing one-row coil with a heating airflow of 145 cfm at an entering temperature of 52 F, a leaving air temperature of 90.5 F, an entering hot water temperature of 180 F, a leaving hot water temperature of 141.1 F, and a heating capacity of 6.05 MBH. The zone heating requirement is 5.4 MBH. When the same coil is supplied with 160 F entering hot water, the resulting heating capacity is 4.5 MBH (see Run 1 in Table 2).
Since the resulting heating capacity of Run 1 is less than the required heating capacity, further evaluation is required. In this particular case, the heating airflow needed to be increased to get a valid coil selection. This is reflected in Run 2 with an airflow of 220 cfm and a heating capacity of 5.48 MBH. The resulting leaving water temperature is in the desired range for a condensing boiler system, while the required water flow has been reduced. The branch piping to the coil, as well as the coil, can be reused. While an increase in airflow for a single coil will not have an appreciable impact on the fan energy consumption, the air side of a system with multiple heating coils can’t be ignored. Any resulting change in fan energy would need to be included in the overall energy analysis of the hot water system as well as confirmation of the heating load and coil rows/capacity.
Control valves at the coil should be two-way modulating type valves. This will allow the variable flow distribution pumps to operate at lower speeds when the building is not at peak heating load. In retrofit applications, when changing from a constant volume noncondensing system to a variable volume condensing system, all existing three-way valves will require replacement. Balancing valves are not necessary at the coil in variable flow systems using two-way valves. The use of balancing valves in this type of system results only in increased system pressure drop with no associated improvement in flow control. In the event the system serves a critical load that requires immediate hot water, use a small two-way valve and temperature sensor at the end of the run serving the load instead of a three-way valve. Modulate the valve to maintain the supply temperature in the run to the critical load at least 10 F lower than the system supply temperature.
System control
Now that the efficiency of the components has been maximized, the system must be controlled with these efficiencies in mind. The hot water plant should be provided with a Btu meter consisting of a flow meter and matched temperature sensors to measure the distribution system load. The fuel supply to the boilers should also be metered. The plant efficiency should be calculated from this data, displayed on the operator’s control system interface, trended, and archived.
Maintaining a constant hot water supply temperature is no longer desirable if it results in the condensing boiler operating in a noncondensing condition. The supply temperature should be reset based on system demand and commanded hot water control valve positions. Lower system demand can be satisfied by a lower supply temperature to keep at least one hot water control valve in the system 85% to 90% open. Lowering the supply temperature may also minimize use of the bypass valve to maintain minimum flow through the boiler.
Boiler staging needs to take the part load efficiency of the condensing boilers into account. This can be accomplished by programming the efficiency versus hot water return temperature data for each stage of firing into the control system. Using this information in conjunction with the system load measured by the Btu meter, the most efficient boiler staging can be determined. Most boiler manufacturers offer boiler plant controllers that will stage the boilers to optimize the overall boiler efficiency. These controllers must be integrated into the building control system, which will sometimes require a gateway.
The variable speed pumps need to respond to the load fluctuations in the system. This has historically been done using a differential pressure sensor somewhere near the end of the distribution system. Direct digital control (DDC) systems can easily determine the most demanding load by using the commanded hot water valve position. When valve position is used for pump control, the differential pressure sensor can be located in, or near, the heating plant, making it more cost-effective to wire the sensor directly to the plant controller. The differential pressure setpoint should be reset to maintain the most open valve at 85% to 90% open. This will minimize system pumping energy.
The valve position control signal can also be sent directly to the pump variable frequency drive (VFD) to control pump speed. In that case, it is recommended that a differential pressure sensor be provided at the heating plant and integrated into the DDC system for use in troubleshooting, should it be required. In all cases the minimum flow required by the boiler must be maintained. As many terminal unit reheat coil valves are sized for small flow rates, it may take multiple valves being open to maintain boiler minimum flow rates. A small circulating pump at the boiler is also an option, but may add to the energy use and should be evaluated against first and operating cost.
DDC systems can easily interface with a manufacturer’s boiler controllers to provide information that was previously not readily available. Stack temperature, percent fire, and boiler outlet temperature data can be used to create baseline data during system commissioning. Periodic comparisons to the baseline can be generated by the control system to assist the facility staff in the early detection of heat exchanger performance degradation. Maintenance alarms based on this information should be provided as part of the controls specification and plant sequence of operation.
Cost considerations
While it is a noble goal to design the most efficient system possible, very few clients are that altruistic. Condensing boilers have a cost premium over a comparable size noncondensing boiler. Depending on the base boiler used for comparison, the cost premium can be as low as 20% to as much as four times the base boiler cost. Detailed energy savings calculations and a lifecycle cost analysis should be done to compare hot water system options and arrive at a final recommendation.
One way to mitigate cost is to evaluate a hybrid boiler plant that combines both types of boiler technology. A simplified control schematic is shown in Figure 2. (Note that the figure is not intended to reflect all valves and trim necessary for a complete system.) The hybrid plant maintains the variable flow primary pumping through the condensing boilers while side streaming the noncondensing boiler off of the hot water supply main downstream of the condensing boilers. A constant volume pump is provided for the noncondensing boiler. Use of an ECM pump should be considered as it will allow the proper flow to be dialed in while saving energy. In this arrangement the condensing boilers operate first, taking advantage of their better part load performance. As the system load exceeds the capacity of the noncondensing boiler, the condensing boiler discharge temperature can be reset to provide a relatively constant inlet temperature to the noncondensing boiler. This ensures that the minimum inlet temperature to the noncondensing boiler is always met and the boiler remains base loaded while the noncondensing boilers continue to operate at part load.
A hybrid plant may also be a good option in a retrofit application for systems where the existing noncondensing boiler is oversized and short-cycling. The number of condensing boilers can be minimized while improving overall plant performance and extending the operating life of the existing boiler.
With this type of plant, maximum flow through the condensing boilers requires consideration. There will be times when the system load requires more flow, or load, than can be handled by the condensing boilers, resulting in reduced boiler performance. This can be addressed by providing a modulating (diverting) bypass around the condensing boilers. The bypass valve is modulated based on the differential pressure across each condensing boiler. The discharge temperature of the condensing boilers is then reset to provide a minimum mixed water temperature to the noncondensing boiler of 140 F.
With a better understanding of maximizing the component efficiencies and operating the system more efficiently, it is possible to design efficient hot water systems while meeting the client’s need for cost effective solutions.
Cynthia Callaway, PE is a senior mechanical engineer at P2S Engineering Inc. She has more than 30 years of experience in mechanical/process project design and commissioning with extensive experience in energy analysis, trend data collection/analysis, and development of energy conservation measures.