By making correct pump and piping selections, systems can operate at or near peak efficiency, avoid cavitation, and maintain a long service life. With each system type a multitude of options are available to a designer or engineer; but within these, the best option must be selected for a given application.
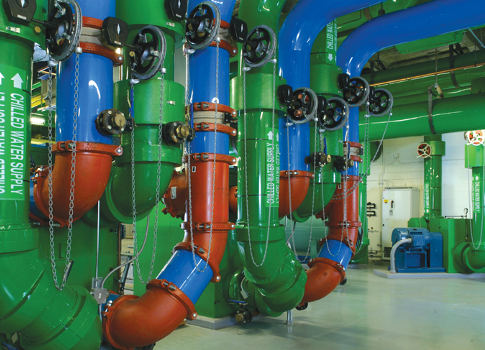
Learning Objectives:
- Explain the types of pumps used in HVAC and plumbing systems.
- Model calculations for pump speed, size, and curve selection.
- Appraise energy-efficient solutions.
Waterside pumping and piping systems are typically considered less complex and easier to apply/design than their airside counterparts. With greater density and heat transfer capacity, water can carry the same amount of energy through a much smaller conduit than air. This allows pipes to route through buildings with fewer clashes, and easier coordination with other trades within congested plenum spaces than the same energy transferred within ductwork.
A 2-in. chilled-water pipe is typically simpler to route through a congested ceiling space than a 30-in. equivalent duct (using a 16°F ΔT for chilled water and 20°F ΔT for air at 2.5 ft/100 ft pipe friction and 0.08 in. wc/100 ft.
With these arguments, people are led to believe that water systems require less effort in design and need less skill to implement than airside systems. These assumptions, however, hide the vast array of pumps available to choose, or the shortened operational life that can occur from improper engineering selections.
Pump construction and material types
A centrifugal pump is the standard pump type used within commercial buildings for both HVAC and plumbing systems. These pumps are made of a volute casing that houses the impeller, which rotates to draw water from the suction eye and discharge it radially out through the impeller vanes (perpendicular to the drive shaft). The impeller is attached to the drive motor either directly or through a separate drive shaft (closed- or split/flexibly coupled, respectively).
The water is directed out through the discharge nozzle with a very small quantity of water recirculating back at the cut water (resulting in pump inefficiencies as this clearance increases with reductions in impeller diameter for a specific volute casing size).
The volute and impeller can be constructed of differing materials depending upon the requirements of the system. The typical material types for different HVAC and plumbing systems are as follows:
HVAC: chilled, heating, and condenser water
Standard materials include a cast iron volute casing and a bronze impeller, referred to as a bronze fitted pump. These material types are typically only usable for nonpotable, treated water systems (controlled pH and chemical concentrations), where corrosion is unlikely, and more of the oxygen is removed from the system (either through standard air vents in a closed-loop system or through an air separator in an open-loop condenser water system). The typical pH requirements of chilled-, heating-, and condenser-water systems are from 7-9 (slightly alkaline), with total dissolved solids (TDS) less than than 1,500 ppm.
Review these values with the specific equipment to be used within the system, as they may vary depending upon the manufacturer. The TDS requirements are typically used for condenser-water systems to help define the specific cycles of concentration that are allowable for the water system. This is the number of times the water is able to recirculate through the piping, pumping, and cooling tower system before it is required to be drained out of the system and replaced with freshwater and further chemical treatment.
Plumbing: potable cold, hot, and hot-water recirculation
The standard material used in potable water booster pumps is stainless steel volute and impeller. This is due to the potable-water code requirements for low lead content within the system, as well as high levels of oxygen present within potable water and limited or no water treatment that is completed.
Though potable-water treatment in buildings is not common, some designs introduce chemicals such as chlorine dioxide, silver ions, or other means of controlling legionella bacteria beyond heating the system to approximately 140°F. Caution is recommended when providing additional treatment of potable water within commercial buildings. In many instances, these systems must be permitted and approved by the authority having jurisdiction (AHJ), as these systems can become a public health hazard if not properly implemented or maintained.
An item that may require additional selection and scheduling with a pump is the respective mechanical seals. The mechanical seal provides the watertight seal between the volute casing and the motor drive shaft where it must connect to drive the impeller. Pump manufacturers provide a standard seal with each pump, but other options are available from the factory. Seal types can be as simple as a stuffing box packed with coated cord until it seals the opening between the casing and drive shaft. These are typically only used for fire-sprinkler water pumps or in some cooling tower applications where high levels of TDS are present. The other typical mechanical seal uses a stationary seat and a rotating seal ring pressed against each other by a spring along with an O-ring elastomer.
There are various types of materials available for these two parts, depending upon cost and type of water in the system, from carbon/ceramic to silicon carbide/silicon carbide (SiC/SiC). SiC/SiC seals are effective with higher levels of total dissolved solids, abrasive resistance, and higher-temperature water systems (when paired with the correct O-ring, Buna, Viton, or EPDM [ethylene propylene diene monomer rubber], as required for the temperature of liquid).
One side note to mention regarding centrifugal pumps is the misconception of force when talking about pump operation and water flow. The "centrifugal force" that is often talked about in pump books and literature, which is stated as the force keeping an object following a curved path from moving away from the center, is actually a fake force in physics terms. If you remember your physics classes, centrifugal force is actually the result of the inertia of the object trying to resist the change in movement. The actual force attributed to this phenomenon is centripetal force, which is the force that keeps an object in a rotational path instead of moving in the vector direction of velocity at a specific point. Centripetal force acts in the direction perpendicular to velocity, between the object and the center of rotation.
Pump selections
Choosing an HVAC pump for a specific duty point has been well covered in previous articles such as "Selecting an HVAC Pump" (May 2015). The article includes calculations for expected system pressure drop (total dynamic head) along with the flow requirements based upon the heat-capacity requirements. Please review the article for detailed information regarding net-positive suction head (NPSH available of the system greater than the NPSHR [required] of the specific pump), as well as calculating friction loss in a piping system for both closed- and open-loop systems.
Closed-loop systems: These typically are HVAC chilled- and heating-water piping systems that are not open to atmosphere. The required pressure loss of the piping system takes into account only the full piping loop (distance to the farthest coil multiplied by two for supply and return piping) along with all of the equipment and accessory losses in the system including valves, coils, strainers, etc.
For large piping systems, the friction loss through elbows is typically considered as an additional 25% to 35% of the straight length of piping (125% to 135% total straight piping). For small systems, this value can be up to 75% to 100% of the straight pipe length (175% to 200% total). The physical elbows can be counted as well, but, as engineers know, most piping designs are not installed identically to the contract drawings.
Using percentages from the straight length provides a gauge of the overall system schematic, but entry-level designers/engineers should calculate the full pressure drop elbow by elbow and piece by piece for a few systems before they can be comfortable with using percentage rules without issues.
The standard pressure drop and velocity used to size closed-loop piping systems are 2.5 ft/100 ft and a maximum of 8 fps (whichever is more stringent for a pipe size). These are rules of thumb, but are based upon empirical data from previous system designs. The friction-loss limitation assists in maintaining flow at the farthest fixtures and maintaining velocities below the threshold for acoustical requirements where piping is located adjacent to noise-sensitive areas (as defined by acoustical-consultant reports. and the limitation is used for more standard commercial buildings, areas like theater seating may require additional flow restrictions).
These values can be exceeded when present in dedicated mechanical rooms or where the respective terminal unit is located close to the pump discharge, which allows for increased pressure available in the branch circuit. Expected system diversity also should be taken into account, especially for large systems where all areas of a facility should not be occupied simultaneously. This allows the main utility piping to be reduced in size from the theoretical combined flow rate, as only 80% may be used even when the facility is fully loaded.
The static height of the water column (for piping serving towers or high-rise buildings) is only accounted within the working-pressure requirement of the pump. The total dynamic head of the system, along with expansion-tank precharge, is also added to the static height of water for the pump’s working pressure. The typical pump working pressure is 150 psi as standard with 300 psi available as an option in most cases.
An important item to be mindful of when designing a closed-loop piping/pumping system is the inclusion of an expansion tank to compensate for fluid expansion between system fill and equipment operation. This is important for both chilled-water and heating-water systems, as there is always a temperature differential between the filled temperature of the system and the operational temperature. This is typically the difference between the groundwater temperature and the maximum temperature expected in the system.
For an area such as Las Vegas, the groundwater fill temperature is approximately 60°F with a maximum of 85°F for chilled-water systems (when the chillers are not operational and the system is under flushing or the branch is stagnant during summer) and upwards of 180°F for heating-water system supply temperatures with a standard noncondensing boiler system. The precharge pressure of the expansion tank will add approximately 15 psi to the system pressure to maintain enough pressure at the top of the system for correct flow through air handling unit (AHU) coils and other heat-transfer devices that may exist at the farthest point in the system.
Pumps used within closed-loop systems include vertical-inline, end-suction, and horizontal/vertical split-case, though we have recently seen vertical-inline pumps used more frequently in chilled- and heating-water systems due to their lower vibration and floor-footprint requirements within central plants. These include small, medium, and large central plant heating-, chilled-, and condenser-water pumps.
Open-loop systems: Typically, these include plumbing potable-water and HVAC condenser-water systems that have the piping outlet open to atmosphere and intake a larger quantity of freshwater than closed-loop systems. The piping length to the furthest outlet (including elbows, but not the return piping for domestic water systems as the hot-water return system uses its own pump), piping accessories (valves, etc.), and the vertical height of piping all factor into the total dynamic head of the pumping system. All of these values also factor into the working-pressure requirements of the pump along with the minimum pressure required at the outlet.
Because of the pressure differences between open- and closed-loop systems, certain pump types are more useful than others. Vertical multistage pumps are most common for plumbing domestic water booster pump systems. They provide high head with lower flow operation with multiple impellers configured in series to boost the volume of water to higher pressures than would be attainable in a standard single impeller. Condenser-water systems typically use standard HVAC-type pumps with high flow and lower head requirements when the respective cooling towers are installed at a lower level (such as in a detached central plant found on many large central plant system designs).
The standard pressure drop within open systems—specifically plumbing domestic water systems—is defined by the first fixture served and the last fixture served. The typical operational limits for plumbing fixtures is 25 to 30 psi at the lower end (for proper flush-valve operation, though this may be as high as 60 psi for shower operation for certain high-flow body-spray or experience shower applications) and 80 psi at the upper end (for maximum acceptable pressures at flush valves and other fixtures).
The pressure drop per 100 ft can be determined based upon the total length of piping (from the pump to the fixture in one direction) and the difference between the upper and lower pressure limits. This can provide a much higher pressure drop per 100 ft than some closed-loop systems, but designers/engineers also must be mindful of the local-code-limited velocities for domestic cold- and hot-water systems (which may be as low as 5 fps for hot-water systems).
Open-loop systems do not require expansion tanks, but for domestic-water booster pumps, a hydropneumatic tank is commonly provided within the booster-pump skid to reduce the run time and cycling of the pump. This precharged tank is maintained at the system pressure and drawn down by the attached plumbing system before the booster pump is required to start, thereby reducing the number of start/stop cycles required of the pump (this prolongs pump operating life).
Some booster pump manufacturers state that by using a multipump variable frequency drive (VFD) arrangement in a packaged multistage system, the hydro-pneumatic tank is not required. It is still recommended to include the tank unless there are structural issues with the weight of water or space constraints. These tanks are precharged at the system pressure and provide a buffer water volume to prevent continual cycling of the booster pumps (reducing start/stop times per day), which assists in increasing the overall pump longevity.
Impeller trimming
To trim or not to trim? For many years, trimming was clearly the best answer to this question. Trimming is the act of trimming the impeller (reducing its diameter within a fixed-volute casing). This is easily defined on most all pump-performance curves where the curved lines descending from peak efficiency (maximum diameter) are shown to meet specific system duty requirements. For constant-volume systems, trimming the impeller is a typical method of meeting the duty point of the system (total dynamic head and volumetric flow rate) with a standard pump.
The main detriment of trimming the impeller is loss of pump efficiency. This is graphically shown on the pump curve, as the curves move farther and farther from the peak efficiency curve, but the loss of pump efficiency is physically a product of the increase cutwater clearance that allows more water to bypass the discharge outlet and recirculate with the impeller. The other main difficulty with trimming the impeller is if the installed system requires additional head to meet the scheduled flow, the only option is to purchase another larger impeller and retrofit the pump.
For current pump systems where VFDs are common, requirements to trim the impeller are becoming less, which allows systems to reach higher levels of efficiency while maintaining the system flow and pressure requirements. These are not able to fix all situations, but a VFD may allow the pump impeller to remain at its maximum size while reducing the frequency and speed of the pump to meet the required system conditions of flow and pressure.
Pump speed and curve selection
Three main operational speeds are available from pump manufacturers, each with its specific application. These are as follows:
- 1,150 rpm: Used for low-head and high-flow applications, such as condenser-water applications where the cooling towers are installed at grade level just above the level of the pumps.
- 1,750 rpm: Used for most typical pump applications, such as most chilled- and heating-water applications.
- 3,500 rpm: Used for high-head and low-flow applications, such as domestic-water booster pump system applications. Though these may have increased wear on the bearings due to the higher speed operation.
Two types of pump curves are available to designers/engineers as described below with the following definitions and uses:
- Flat curves:
- Flat pump curves are defined as those in which their pump head rises less than 25% from the operational point to the shut-off head.
- Flat curves can offer better efficiencies with variable volume systems.
- Steep curves:
- Steep curves are more conservative when the actual pump head cannot be measured (or calculated) accurately.
- They allow for more variation with pump head while maintaining a similar flow volume.
Flow and friction loss
Two equations that should always be presented when referencing pumping systems are as follows:
Heat flow with chilled/heating water systems.
Where
Q = heat flow (Btu/hour)
Cp = Specific heat of water at 60°F (1.0 Btu/lbs°F)
ρ = Density of water at 60°F (62.37 lbs/ft3/7.48 gal/ft3 = 8.34 lbs/gal)
V = Volumetric flow rate (gal/minute)
ΔT = Temperature differential (°F)
At standard conditions, this simplifies down to the equation with which most engineers/designers should be familiar:
This equation is used with typical chilled-water/heating-water coil selections and provides a direct correlation between the space cooling/heating requirements (provided by heated or cooled air) and the chilled- and/or heating-water piping systems.
Piping friction losses for both closed and open systems.
(Darcy-Weisbach equation)
Where
hL = head loss (ft of water)
f = friction factor
l = pipe length (ft)
D = internal diameter of piping (ft)
V = velocity (ft/second)
g = gravitational constant (32.174 ft/seconds2)
This calculation is not often used with the prevalence of pipe-sizing wheels within engineering offices, but it is very useful when working with nonstandard fluids (glycol solutions, for example).
Energy efficiency conclusions
Energy efficiency for pumps is not well regarded. Oftentimes, a designer will select the quickest pump that meets the required flow and total dynamic head requirements without regard for where the point falls on the pump curve or what size impeller is necessary.
Designers and engineers need to be aware of what the pump curve should look like and what design assumptions they have made that may be influenced or modified for the installed condition. They should pay particular attention to these when reviewing submittals prepared by others.
The commercial building is not a perfect world. Clashes, rerouting, and venue/design changes all happen and can impact the pump selections that may have already been purchased and installed on site. Flexibility and energy efficiency are key.
The presented information is a broad coverage of the types of pumps, construction, materials, performance selections, and others needed to properly calculate and specify a pumping system. Many qualified outlets are available to review further information when it comes to specific scheduled options or pump models available for an application.
Matt Dolan is a senior project engineer with JBA Consulting Engineers. His expertise is in designing complex HVAC and plumbing systems for various building types, such as commercial offices, health care facilities, and hospitality complexes including numerous high-rise guestroom towers and restaurants.